Unlocking the Potential: Everything You Need to Know About Glass-Lined Reactors
Unlocking the Potential: Everything You Need to Know About Glass-Lined Reactors
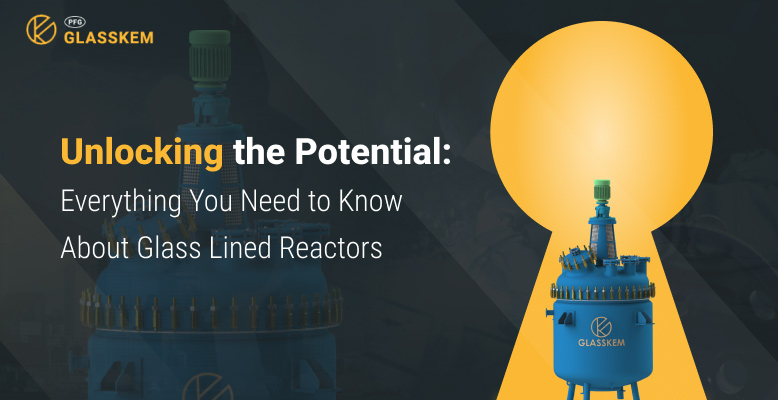
What are Glass-Lined Reactors?
How does the glass-lined reactor work?
Working on the equator will permit the chemicals to enter the proper space and allow them to be mixed via the centrally mounted agitator. This vessel typically has baffles, which ensure a sufficient level of the turbulent inner side to stir with any chemicals that will activate the reactor. Usually, normal chemical reactions will occur with an appropriate catalyst, chemicals, and temperature at the proper time. Hence, the end product could be crystalline or liquid.
What is an MS Glass-Lined Reactor?
It is a type of chemical reactor vessel lined with a layer of glass to protect against corrosion. However, the inner surface is coated with a layer of glass, which will aid you in preventing the corrosion effects of the chemicals involved in the reaction that damage the metal structure of a reactor. Thus, this glass lining provides a non-reactive and corrosion-resistant barrier to deliver secure handling to a wide range of chemicals, which will ease cleaning the reactor after every use.
Types of MS Glass-Lined Reactor
AE Glass Reactor
The glass-lined reactor equipment manufacturer has been completely revolutionized with the AE (advanced enamel) glass reactor. It will make complete use of the enamel technology, which will help you enhance the durability and performance of the glass lining. This will also prevent extreme conditions, high temperatures, and corrosion. However, this reactor type is so famous for the high-demand processes in the chemical and pharmaceutical industries because of the harsh chemicals used in their production. Enamel coating will give a longer service life and optimal performance. Hence, it is a reliable choice for procedures requiring corrosion resistance and mechanical strength in chemical and pharmaceutical manufacturing.
CE Glass Reactor
What is the SS Glass-Lined Reactor?
A stainless steel (SS) glass-lined reactor is used in the chemical and pharmaceutical industries to process substances in controlled conditions. Moreover, stainless steel is used for an outer shell or to develop the reactor to give it strength and durability. Stainless steel will also provide structural support and a glass lining that offers protection against corrosive substances and eases maintenance.
Moreover, these reactors are designed to handle a number of chemical processes for mixing and temperature control and ensure the integrity of the materials being processed. Hence, the glass-lined interior will help prevent corrosion of the reactor metal components, which will extend the glass reactor equipment and help maintain the purity of the processed substances.
Types of SS Glass-Lined Reactor
AE Glass Reactor
An AE glass reactor is being developed, which will make use of chemical substances to help protect it from cohesive materials. However, the AE term identifies “acid-proof enamel,” highlighting a reactor’s ability to protect it from harsh acids. These reactors will provide excellent corrosion resistance against hydrochloric acid, nitric acid, and sulfuric acid. Hence, these reactors are primarily known for their durability, reliability, strength, and ability to maintain product purity in corrosive environments.
SE Glass Reactor
These glass reactors are developed to handle more alkaline, or the base of the chemical processes. This CE, called chemical enamel, describes this reactor as suitable for various chemical applications. It will provide security and protection against harsh corrosion from sodium hydroxide or other alkaline substances. It has a variety of chemical reactions that occur in different pH ranges. Simply put, the CE glass-lined reactor will provide a reliable and versatile solution with solid corrosion resistance even in average temperatures and environments.
Industries Where Glass-Lined Reactors Are Used
This type of reactor is being used in various industries where it will provide protection against corrosion, which is compulsory for handling corrosive materials. Below, let’s look at some sectors where it has been used.
Pharmaceutical Industry
These companies are making use of the glass-lined reactors for the production of pharmaceutical products. However, these reactors are suitable for that process, which will involve synthesizing the active pharmaceutical ingredients and the other pharmaceutical intermediates.
Petrochemical Industry
As the leading company manufacturing glass-lined reactors, we ensure that the vessel we create will help you prevent corrosion and ensure the reliability of our corrosive substances.
Chemical Industry
In the chemical industry, glass-lined reactors are frequently used to synthesize multiple chemicals, specialized chemicals, and pharmaceutical intermediates. They work well with techniques that involve alkalis, corrosive acids, and other reactive substances.
Food and Beverage Industry
In food and beverage applications, glass-lined reactors involve caustic substances like specific food additives or processing aids to store them for a long time.
Conclusion
Glass-lined reactors play an essential role in different chemical and pharmaceutical processes. It will protect the vessel from corrosion, and high temperatures have ease of maintenance and cleaning, which controls an industry’s substances in various climatic conditions.
If you want the best glass-lined equipment manufacturer in Canada, you can connect with the leading company, PFG Glasskem Inc. It ensures that you will meet updated industry standards and provide” a reliable solution for corrosive environments. Hence, these glass-lined reactors will allow industries to store their chemical substances in specialized vessels for reliable and efficient quality.
Unlocking the Potential: Everything You Need to Know About Glass-Lined Reactors Read More »